There are two main methods for threaded hole machining: tap tapping and thread milling. The traditional thread processing method uses tap tapping. In modern thread processing, milling has been gradually adopted to replace the traditional processing method. This paper introduces and compares two processing methods to select the best processing method in actual processing and production, saving resources and reducing waste.
1. Traditional thread processing
The tap is a tool for machining medium and small internal threads, and is grooved in the axial direction. The utility model has the advantages of simple structure and convenient use, and can be operated manually or on a machine tool, and is widely used in production. For small internal threads, the wire is almost the only machining tool. Tapping is a difficult machining process because the tap is almost buried in the workpiece for cutting. The machining load per tooth is larger than other tools, and the tap is very large along the thread and the workpiece. When cutting the thread, it The chips must be contained and excluded. According to the shape, the tap is divided into a straight groove tap, a spiral groove tap and a screw tip tap (tip tap).
(1) Characteristics and applications of straight groove taps. Straight groove taps are shown in Figure 1, which are generally used for carbon steel, alloy steel and non-ferrous metals. It is characterized by the strongest versatility, through holes or through holes, non-ferrous metals or ferrous metals can be processed, and the price is also the cheapest. The blade has good strength, easy grinding, large cutting torque during machining, and poor chip breaking and chip removal capability; the cutting cone can have 2, 4 and 6 teeth, the short cone is used for non-through holes, and the long cone is used for Through hole. As long as the bottom hole is deep enough, the cutting cone should be used as long as possible, so that the teeth sharing the cutting load are more and the service life is longer.
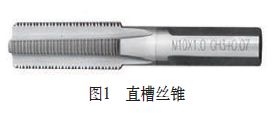
(2) Characteristics and application of spiral groove taps. The spiral groove tap is shown in Figure 2. It is more suitable for machining non-through-hole threads, and the chips are discharged backwards during processing. Due to the helix angle, the actual cutting front angle of the tap increases as the helix angle increases. Processing black metal taps, the spiral angle is chosen to be small, generally around 30°, to ensure the strength of the spiral teeth; processing colored metal taps, the helix angle is selected to be large, and the cutting angle is about 45°.
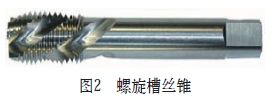
The utility model is characterized in that the spiral groove tap is spiral, and the spiral tap can easily discharge the chips outside the hole by the rising rotation action of the spiral groove, so as to prevent the chip from remaining or being blocked in the groove, and the tap is broken, the blade is broken. The part is cracked, so the life of the tap can be extended and the highest precision thread can be machined. The cutting speed can be increased by 30% to 50% compared with the straight groove tap, and the threaded hole can be processed by a single tap.
(3) Features and applications of screw taps. The screw tap is shown in Figure 3. It works well for non-ferrous metals, stainless steel and ferrous metals. The threaded taps are preferred for through-hole threads. Its characteristic is that the core size of the screw tap is relatively large, the strength is good, and it can withstand large cutting force. Because the front edge of the blade has a special groove and groove design, the chip removal is easy, the torque is small, the precision is stable, and the tap life is longer. Since the screw tap has the function of rotating and discharging the chips, in addition to keeping the groove clean and reducing the resistance during cutting, it can also avoid chip damage and damage the tap, so the screw tap can be used more than the general hand tap. Fast speed to cut high precision threads. The chips are discharged forward when the thread is machined.
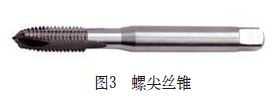
2. Modern threading method - thread milling
(1) Features and applications of thread milling. As a new type of threading process, thread milling has unique advantages and more extensive and flexible use and application compared to tapping. details as follows:
1 processing efficiency is high. 2 Surface quality and dimensional accuracy are high. 3 stability, safe and reliable. 4 a wide range of applications.
Thread milling is a versatile and new type of advanced machining technology, but it also has limitations: 1 requires the use of three-axis CNC machine tools. 2 Although it costs less than taps in batch processing, a single thread milling cutter is more expensive than a tap. 3 Thread milling programming is cumbersome, which is one of the important factors limiting its wide range of applications.
(2) Selection of thread milling cutters. With the popularity of CNC machine tools, thread milling technology is increasingly used in machinery manufacturing. Thread milling is a three-axis linkage of a CNC machine tool. The thread milling cutter is used for helical interpolation milling to form a thread. The tool moves in a circular motion every week on a horizontal plane, and a pitch is linearly moved in a vertical plane.
There are many types of thread milling tools currently in use, and several common thread milling cutters have the following features.
Ordinary machine clamp thread milling cutter. Machine-type thread milling cutters are mainly used for milling large diameter internal threads and for milling external threads. Because the blade is easy to manufacture and the price is lower, the impact resistance is slightly worse than the overall thread milling cutter. Therefore, the tool is often recommended for machining aluminum alloy materials, and its structure is similar to that of a conventional machine-clamping cutter. It consists of a reusable cutter bar and a blade that can be easily replaced. When selecting a machine-type thread milling cutter, the material of the larger diameter shank and the appropriate insert should be selected as much as possible according to the diameter, depth and workpiece material of the thread to be machined. Ordinary multi-blade machine clamp type thread milling cutter is shown in Figure 4.
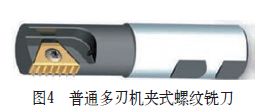
Ordinary integral thread milling cutter. As shown in Figure 5, the integral thread milling cutter is mostly made of solid carbide material, and some are also coated. The integral thread milling cutter is compact and suitable for machining medium and small diameter threads, as well as integral thread milling cutters for machining taper threads. Such tools have good rigidity, especially the integral thread milling cutter with spiral groove, which can effectively reduce the cutting load and improve the processing efficiency when processing high hardness materials. The cutting edge of the integral thread milling cutter is covered with threaded teeth, and the whole thread processing can be completed by machining one thread along the spiral line. It does not need to be layered like a machine tool, so the processing efficiency is high, but the price is relatively expensive. . This type of tap is often used for the machining of small and medium diameter threads.
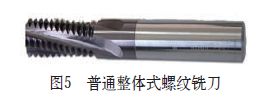
Thread drilling and milling cutter. The thread drilling and milling cutter (see Figure 6) is made of solid carbide and is a high-efficiency machining tool for medium and small diameter internal threads. The thread drilling cutter can complete the drilling of the bottom hole, the hole chamfering and the internal thread machining at one time, reducing the number of tools used. However, the disadvantage of this type of tool is its poor versatility and its high price. The tool consists of a drilled portion of the head, a threaded milling portion in the middle, and a chamfered edge 3 at the root of the cutting edge.
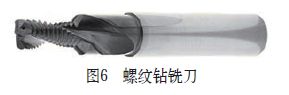
The diameter of the drilled part is the bottom diameter of the thread that the tool can machine. The thread processing process is shown in Figure 7. Due to the limitation of the diameter of the drilled part, a thread drilling and milling cutter can only process one thread of internal thread. When selecting a thread drilling and milling cutter, not only the threaded hole size to be machined, but also the effective machining length of the tool and the depth of the machined hole should be considered. Otherwise, the chamfering function cannot be realized.
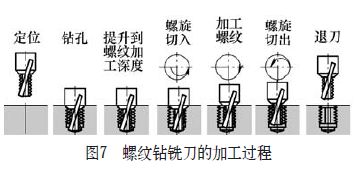
Thread milling tool system. System versatility and high efficiency are a prominent contradiction of thread milling cutters. Some tools with composite functions (such as thread drilling and milling cutters) have high processing efficiency but poor versatility, while versatile tool efficiency is often not high. In order to solve this problem, a modular thread milling tool system (see Figure 8) has been developed. The tool consists of a shank, a boring chamfering edge and a universal thread milling cutter. Different types of boring can be selected according to the processing requirements. Chamfered edge and thread milling cutter. This tool system has good versatility and high processing efficiency, but the tool cost is high.
(3) Thread milling problems and solutions. Thread milling cutters, like other milling cutters, encounter blade wear, chipping and built-up edge during milling. The attached table is a common problem in thread milling and the corresponding solutions.
3. Conclusion
In this paper, based on the two machining methods of threaded hole machining, the selection of the tool when machining the thread is analyzed. The characteristics of each threaded hole machining tool, the performance of the tool and the applicable occasions are mainly introduced. Both the traditional processing and the modern processing of the thread have their own advantages and disadvantages. Although the traditional thread processing method has low precision and easy tool wear, it has high practicability; modern thread processing method has high surface quality and high precision, but the processing cost is expensive, and the numerical control programming is cumbersome. In actual production and processing, comprehensive consideration should be given to the process. It is preferable in many aspects such as properties, usability, and economy, thereby improving processing efficiency, reducing cost, and manufacturing high-quality, high-precision threaded holes.